Display Tab overview
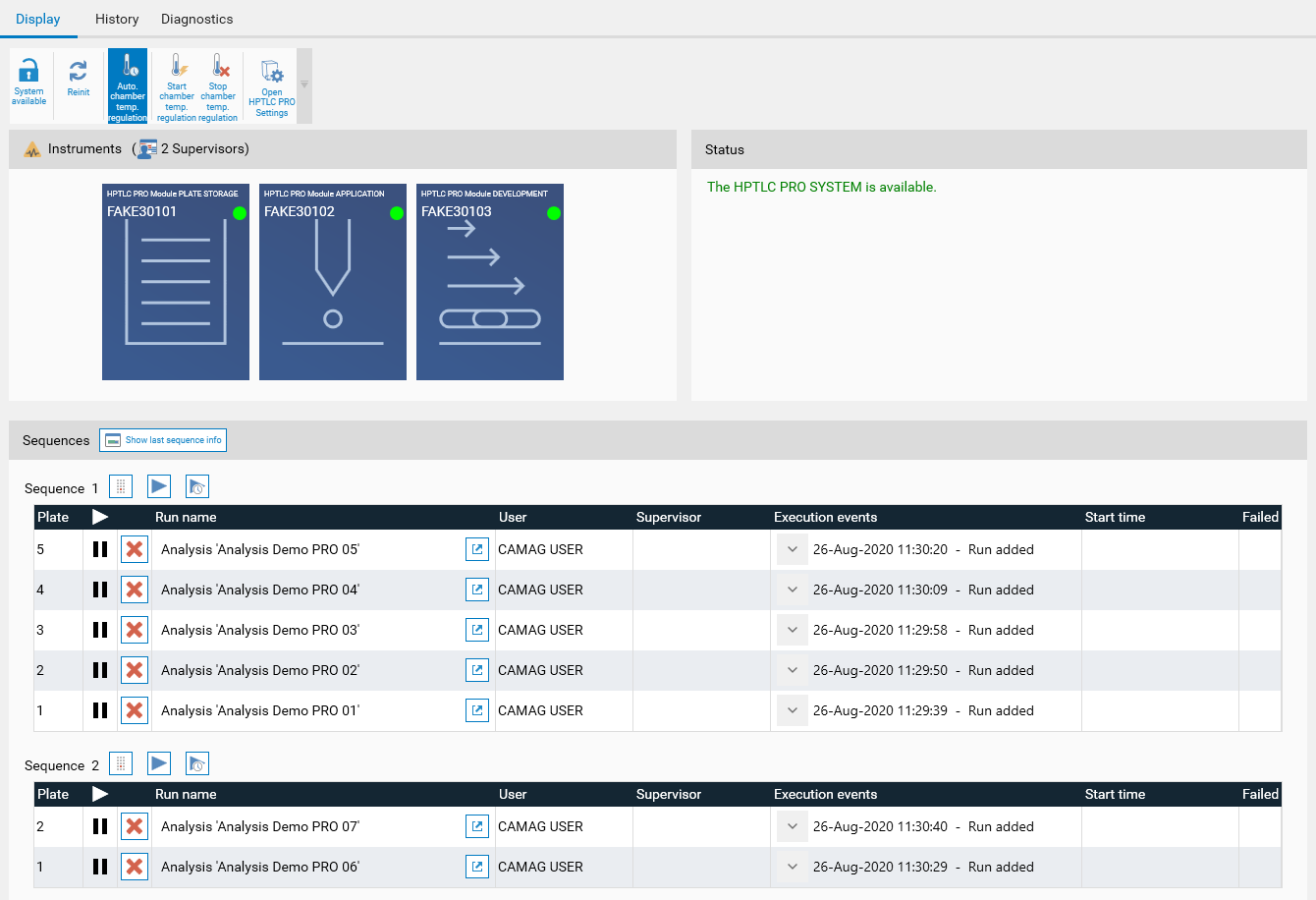
The Display tab shows the current status of the CAMAG® HPTLC PRO SYSTEM. More detailed than the New CAMAG® HPTLC PRO SYSTEM Configuration window, it is though limited to a single HPTLC PRO SYSTEM and displays the runs information.
Toolbar
Lock/unlock the HPTLC PRO SYSTEM. A supervisor typically locks the HPTLC PRO SYSTEM to prevent the execution of new sequences in order:
To perform management tasks:
Change module consumables in Properties tab (see Consumables validation)
Run manual control functions in Manual control tab
Perform module diagnostics in Diagnostics tab
To resolve errors related to carriers or to the modules themselves
The execution of sequences (see Execution of a sequence) requires the HPTLC PRO SYSTEM to be available. It is not possible to lock the HPTLC PRO SYSTEM during the execution of a sequence.
The HPTLC PRO SYSTEM will reinitialize, useful after an external change (like removing a carrier). See Understanding the HPTLC PRO Module and CAMAG® HPTLC PRO SYSTEM initialization
Open the CAMAG® HPTLC PRO SYSTEM Configuration view
If a CAMAG® HPTLC PRO Module DEVELOPMENT is present, this feature (which is activated by default) triggers the chamber temperature regulation periodically (each 15 minutes) when the System is available. Consequently, the supervisor can lock the System to “suspend” the temperature regulation. This is suitable when users want to reduce regulation time as much as possible. The drawback is that the module may be overused and generate noise. Note that when the automatic chamber temperature regulation is activated/deactivated, a corresponding log entry is written in the HPTLC PRO SYSTEM History.
Use these functions to control the chamber temperature regulation manually. These functions are accessible even if the automatic mode is activated. Disabling the automatic chamber temperature regulation and working only with manual functions is suitable when the supervisor knows when sequences will be launched and when he wants to manage the temperature regulation himself, or simply when the timing is not critical (the module will still perform a chamber temperature regulation if necessary at the beginning of each development step).
Modules
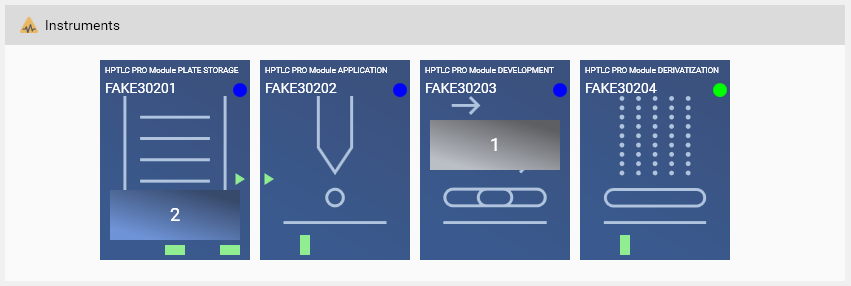
In addition to the display of the HPTLC PRO Module statuses, a schematic view of the carriers is displayed on the HPTLC PRO SYSTEM.
In the example shown by the previous capture, a sequence was executed with 4 runs. When the screen capture has been taken, the plate for the first run was being developed in the DEVELOPMENT module, while the second run was starting (carrier on the conveyor of the PLATE STORAGE module, moving to the APPLICATION module). Additionally, the display adds more precise information about the placement and the movements of carriers:
Green rectangles show positional statuses:
The status of the carriers detectors for the conveyor (horizontal layout, 3 detectors for each module),
The position of the feeder (vertical layout, essentially used to know whether the feeder is in feeding position).
Green triangles show moving directions:
Whether the modules conveyors are moving carriers between modules,
Whether the feeder is moving between the feeding position and the processing position.
The carrier is here identified by a corresponding color and number in the runs sequence.
By right-clicking on the module:
The carrier can be manually ejected by using the Try to eject carrier function, which places the carrier on the conveyor. The user will have to open the door of the concerned HPTLC PRO Module to remove the carrier. For a CAMAG® HPTLC PRO Module PLATE STORAGE, the carrier is moved to the manual unloading position of the module at the left side and the user will have to unload it manually. This may be necessary after a reset, as the run was interrupted but the carrier remains in the HPTLC PRO SYSTEM: the Conveyor Manager signals it as unexpected.
The Reset module feature can be interesting in case of a critical error received from the module. If the module was performing a step of a given run while hitting the Reset module entry, the run is interrupted but the other runs on the HPTLC PRO SYSTEM can be recovered, while a reset of the HPTLC PRO SYSTEM causes the interruption of all current runs.
The Force end of initialization can be used to initialize the feeder of the module manually (once the internal initialization of the module is finished, see Understanding the HPTLC PRO Module and CAMAG® HPTLC PRO SYSTEM initialization and Status colors). This can be useful because the feeders are not initialized when modules are switched on while the HPTLC PRO SYSTEM is locked or offline. The supervisor can then initialize the feeder of a given module manually, for example to perform the diagnostics (see Diagnostics tab), without having to unlock the HPTLC PRO SYSTEM and then lock it again.
The Show last activity is a shortcut to the History tab, in Table display mode, preconfigured to show only the last items related to the module.
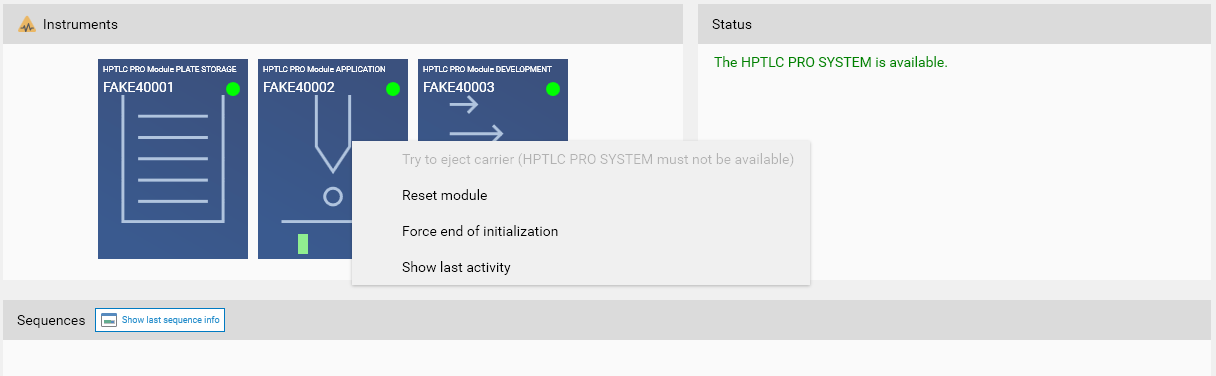
Status
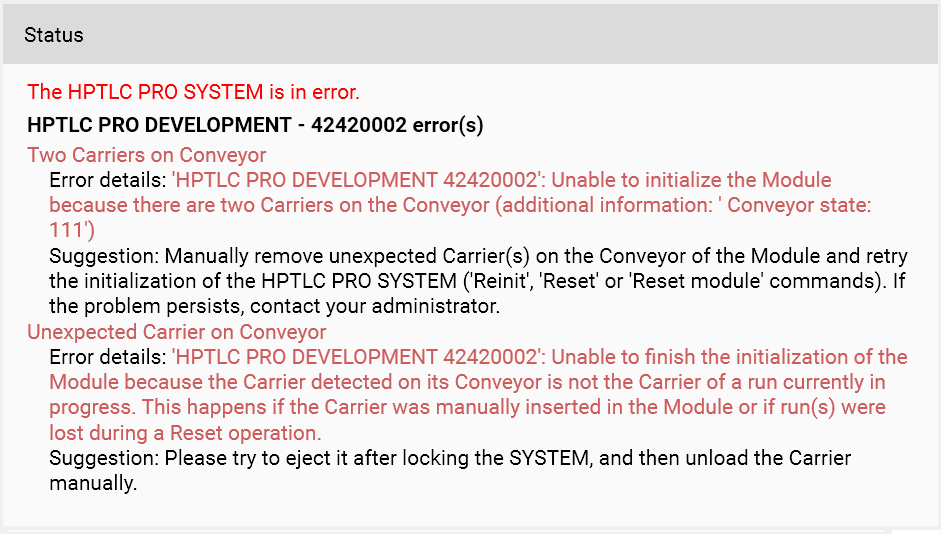
The status of the HPTLC PRO SYSTEM and any HPTLC PRO Module error are display here. Each error is associated with details including contextual information and suggestions on how to resolve the error. For example in the previous capture, two carriers were manually placed on the conveyor of the HPTLC PRO Module DEVELOPMENT and an initialization tentative was made by hitting the Reinit button.
Sequences
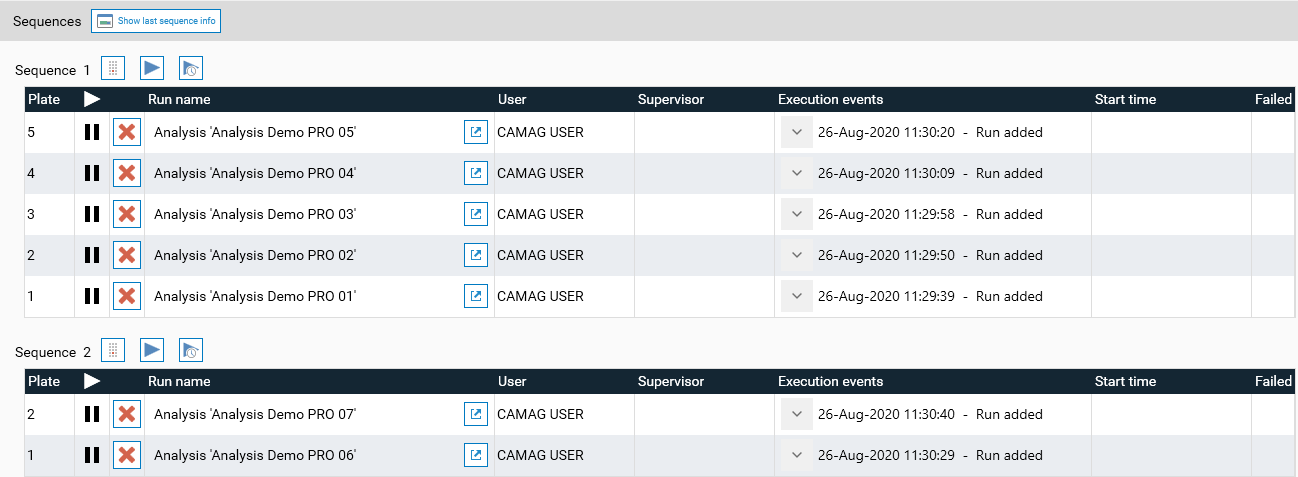
All the runs are grouped into sequences of this HPTLC PRO SYSTEM. Hit the button to display the last executed sequence information (see Last sequence info).
For each sequence, the user can:
See the rack configuration of this sequence.
Execute the sequence. See Execution of a sequence
Execute the sequence at a specific time. See Execution of a sequence
Note
A sequence can contain up to 5 runs.
The different columns give more information about each run.
Plate: a number to identify the order (and the corresponding row in the stacker if a CAMAG® HPTLC PRO Module PLATE STORAGE is used) and a color code to help identify the plate/carrier in the Instruments view above (automatically generated)
Running status: either running or not
Important
A run is marked as running as soon as the sequence execution has started.
Abort the run (only possible if the sequence is not running, otherwise must be done from the analysis.)
Run name: name of the corresponding analysis. The link will open the analysis
User: which visionCATS user added the run to the sequence
Supervisor: which visionCATS user executed the sequence and will be notified
Execution events: like in the Chromatography tab of the analysis during the execution of the run, the full list of execution events is displayed
Start time: when the run was selected for execution
Failed: display runs having an unrecoverable error (for example if a carrier is blocked during a movement on a conveyor). Failed runs are removed from the HPTLC PRO SYSTEM the next time it is initialized (for example by reenabling it or by using the Reset function)
Note
The view can also display the requested consumables when the sequence execution is started (see Consumables check).